

- #MAGMASOFT CENTRIFUGAL CASTING FULL#
- #MAGMASOFT CENTRIFUGAL CASTING SOFTWARE#
- #MAGMASOFT CENTRIFUGAL CASTING TRIAL#
- #MAGMASOFT CENTRIFUGAL CASTING FREE#
SALSA 3D is being gradually integrated into the ESI Casting Simulation Suite, with the aim of offering a software combination that helps maximize productivity, reduce development time and improve the quality of parts. This potentially delivers significantly increased yield and reduced die development time and the filling system can be validated using ProCAST or QuikCAST. The simulation results showed that the filling pattern was not optimal. When the die arrived at Aallied Die Casting, the team was able to analyze the runner and gating system using MAGMASOFT. It assists in designing gates, runners and overflows by controlling the maximum gate velocity and thickness based on the available pressure machine. Aallied Die Casting (Rutherfordton, NC), a division of RCM Industries, selected MAGMASOFT casting simulation technology to meet this challenge.

The task is to set up the feeder system and the pattern lay-out of a cast iron part to increase the yield and the number of parts in the sand mold. SALSA 3D helps calculate and size, gating and running systems for the High Pressure Die Casting process. The basic theory of the numerical simulation of casting and casting process, also the development and application of numerical calculations in the foundry engineering. In this presentation, we will show the benefit of using design optimization in a real casting problem.
#MAGMASOFT CENTRIFUGAL CASTING FULL#
ProCAST manufacturing casting tools are some of the most powerful in the industry today, and the robust ProCAST engineering gives you the tools to perform evaluations of all casting processes, for all castable alloys.Ĭheck out the full casting suite brochure. ProCAST software, based on powerful Finite Element Technology, is well suited to also predict distortions and residual stresses and can address more specific processes like semi-solid, core blowing, centrifugal, lost foam and continuous casting. ProCAST simulation software offers an extensive suite of modules and foundry tools to meet your most challenging industrial requirements. Using ProCAST allows for easier engineering and manufacturing throughout the process. With its finite element technology, it also predicts complex issues like deformations and residual stresses and comprehensively addresses most castable alloys and most casting processes like sand castings, die castings, investment castings, and multiple variants associated with these processes.ProCAST software is an advanced and complete casting processes simulation tool which is the result of more than 20 years of collaboration with major industrial partners and academic institutions all over the world.
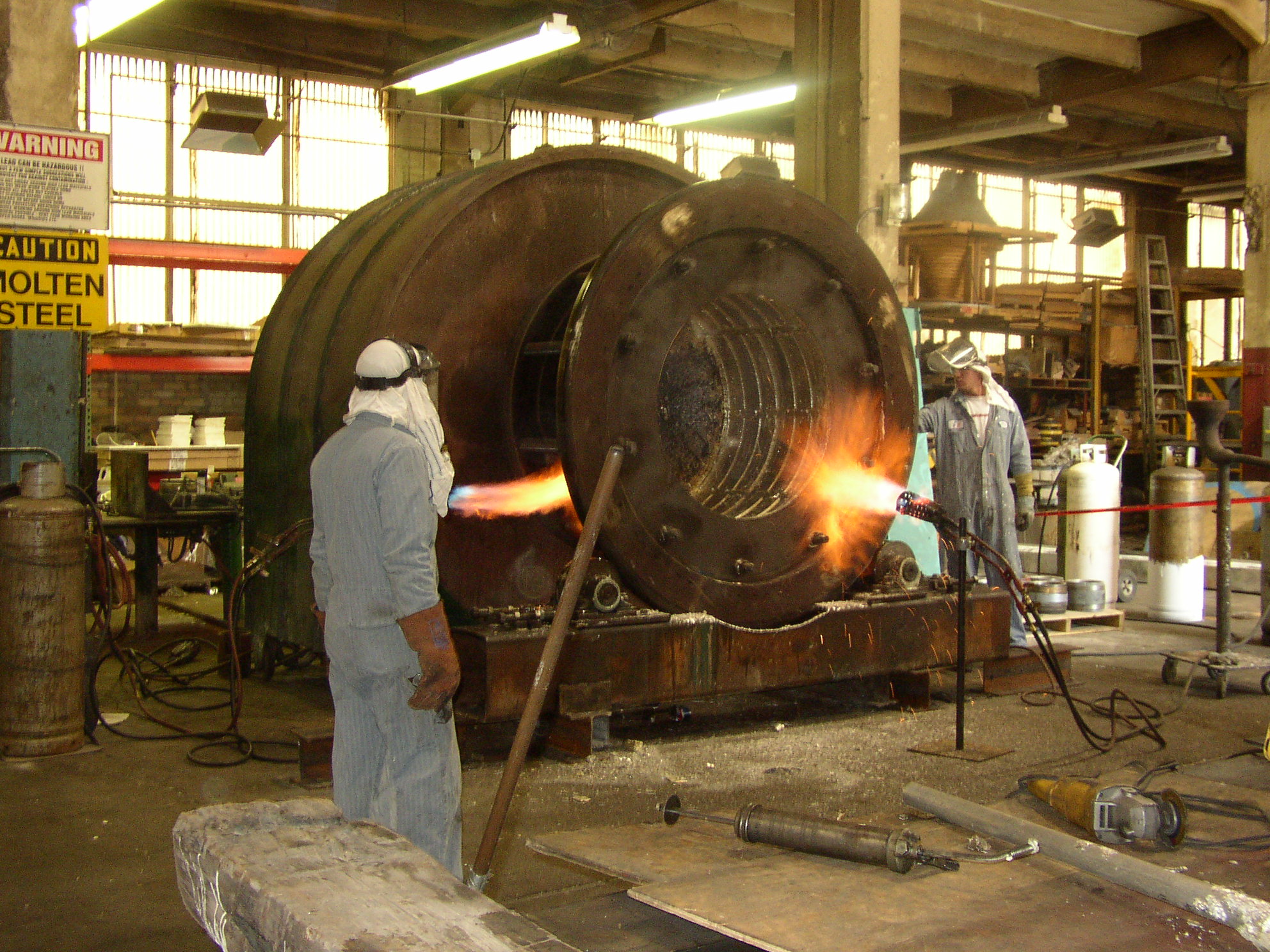
For decades, customers have relied upon ProCAST as their go-to tool for the casting basics – filling, solidification, and porosity prediction.
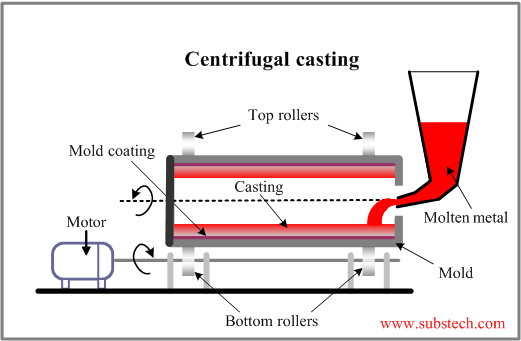
With ESI ProCAST you can cast your parts right the first time, every time –meeting your deadlines and never wasting money on scrap parts or late redesigns. Accurate prediction and quantification of defects and process design are imperative in order to ‘get it right’ during production trials. Simulation allows for virtual testing early on in the development stage.
#MAGMASOFT CENTRIFUGAL CASTING TRIAL#
And because the trial period in the casting development schedule is underestimated, it is imperative to get your gating design to be robust against process variations before arriving at the testing phase. Competences are paper machinery components as well as other non-related industry applications.
#MAGMASOFT CENTRIFUGAL CASTING FREE#
With your deadline staring you in the face, you can either ship the parts and undoubtedly deal with an unhappy customer or go back to the design stage and try to identify the problem, correct it, and hope it is finally free from defects. Production comprises high-quality iron grades (grey and nodular iron) with the first casting cast in 1948. The casting layout is discretized using a cubical mesh. With a total casting weight of 10 kg and S value of 1.85, the pouring time was found to be 5 seconds. Your first off-tool parts are finally available, only for you to realize they contain pinholes, shrinkage, or hot spots. The values of S are 1.63, 1.85, and 2.20 for a casting thickness range of 2.5-3.5 mm, 3.5 to 8 mm, and 8 to 15 mm respectively 14.
